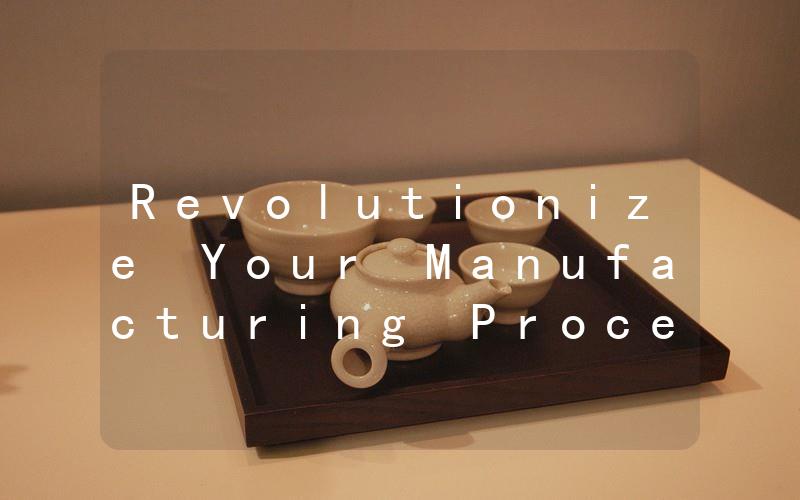
Manufacturing processes have come a long way over the years, and with the advent of new technologies, it has become easier than ever to produce high-quality products with efficiency and precision. One such technology that has revolutionized the manufacturing industry is vacuum forming. Vacuum forming is a process that involves heating a sheet of plastic until it is soft and then using a vacuum to pull the plastic over a mold, creating a three-dimensional shape. This process is used to create a wide range of products, from packaging materials to automotive parts. In this article, we will explore how a high-quality vacuum forming machine can revolutionize your manufacturing process.
Here to introduce you Belief parking heater which made in China with good quality and low price, exported to more than 40 countries, selling worldwide, support oem, welcome to consultation and cooperation.
What is Vacuum Forming?
Vacuum forming is a manufacturing process that involves heating a sheet of plastic until it is soft and pliable. The plastic is then placed over a mold and a vacuum is used to pull the plastic down over the mold, creating a three-dimensional shape. Once the plastic has cooled and hardened, it is removed from the mold and trimmed to the desired shape.
Vacuum forming is a versatile process that can be used to create a wide range of products. It is commonly used to create packaging materials, such as blister packs and clamshells, as well as automotive parts, such as dashboards and interior trim. Vacuum forming is also used in the production of toys, signage, and even medical devices.
The Benefits of Vacuum Forming
There are several benefits to using vacuum forming in your manufacturing process. One of the biggest advantages is the cost savings. Vacuum forming is a relatively inexpensive process compared to other manufacturing methods, such as injection molding. This is because the molds used in vacuum forming are less expensive to produce than injection molds.
Another benefit of vacuum forming is the speed of production. Vacuum forming machines can produce parts quickly and efficiently, making it an ideal process for high-volume production runs. Additionally, because vacuum forming is a relatively simple process, it can be easily automated, further increasing production efficiency.
Finally, vacuum forming allows for a high degree of design flexibility. Because the molds used in vacuum forming are made from a variety of materials, including wood, foam, and aluminum, they can be easily customized to create unique shapes and designs. This makes vacuum forming an ideal process for creating complex parts with intricate shapes and details.
Choosing the Right Vacuum Forming Machine
When choosing a vacuum forming machine for your manufacturing process, there are several factors to consider. One of the most important factors is the size of the machine. The size of the machine will determine the size of the parts that can be produced. It is important to choose a machine that is large enough to accommodate the parts you need to produce.
Another factor to consider is the type of material that will be used in the vacuum forming process. Different materials require different heating and cooling times, so it is important to choose a machine that can accommodate the specific materials you will be using.
Finally, it is important to choose a machine that is reliable and easy to use. Look for a machine that is made from high-quality materials and has a user-friendly interface. Additionally, choose a machine that comes with a warranty and good customer support.
Conclusion
Vacuum forming is a versatile and cost-effective manufacturing process that can be used to create a wide range of products. By choosing a high-quality vacuum forming machine, you can revolutionize your manufacturing process, increasing efficiency and productivity while reducing costs. When choosing a vacuum forming machine, consider factors such as size, material compatibility, and ease of use. With the right machine, you can take your manufacturing process to the next level.